- Messages
- 20,228
- Location
- Springfield, Missouri
I've been spending a little time looking at reviews of some of the current consumer hand held 3d scanners on the market lately. There are several out there and showing promise as a viable option for a small business or fabricator to use for scanning and making products that accurately fit first time from the scans made. Most of the latest ones are touting .1mm accuracy, which isn't bad.
The iPhone scan app I've been playing with has yielded decent results, but the lidar sensor it uses isn't as accurate as some of the structured light and laser scanners available.
From what I've also seen, the software for the scanner itself plays a huge role in the ease of use and quality of the scan.
Out of all the ones I've watched reviews on (almost all below), the Creality Scan Ferret and Shining 3d Einstar stood out the most.
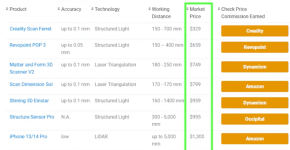
I really was leaning towards the Shining 3d Einstar. The reviews were good and the software really stood out for ease of use. It however did require more of a gaming level of computer for the processing of the scan, which would have added another $1k to the entry price for me. So, I decided to take the plunge on the Creality Scan Ferret Pro version as it is able to scan objects up to 2 meters in size. The software works on mobile, laptop, and desktop devices. Obviously it won't do the same scale of work as the Einstar scanner, but I think it will do what I'm wanting to do with it.
Some of the use cases I have in mind are gun stocks for the cnc rotary, scanning some parts of my tractor and truck to have accurate models to design accessories for, and for many 3d printing projects.
It outputs OBJ, STL, and PLY files, so can import into Fusion360, Meshmixer, Blender, and other software programs for editing.
I'll post up results as I get more experience with it. It should be here early next week.
The iPhone scan app I've been playing with has yielded decent results, but the lidar sensor it uses isn't as accurate as some of the structured light and laser scanners available.
From what I've also seen, the software for the scanner itself plays a huge role in the ease of use and quality of the scan.
Out of all the ones I've watched reviews on (almost all below), the Creality Scan Ferret and Shining 3d Einstar stood out the most.
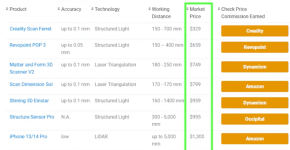
I really was leaning towards the Shining 3d Einstar. The reviews were good and the software really stood out for ease of use. It however did require more of a gaming level of computer for the processing of the scan, which would have added another $1k to the entry price for me. So, I decided to take the plunge on the Creality Scan Ferret Pro version as it is able to scan objects up to 2 meters in size. The software works on mobile, laptop, and desktop devices. Obviously it won't do the same scale of work as the Einstar scanner, but I think it will do what I'm wanting to do with it.
Some of the use cases I have in mind are gun stocks for the cnc rotary, scanning some parts of my tractor and truck to have accurate models to design accessories for, and for many 3d printing projects.
It outputs OBJ, STL, and PLY files, so can import into Fusion360, Meshmixer, Blender, and other software programs for editing.
I'll post up results as I get more experience with it. It should be here early next week.